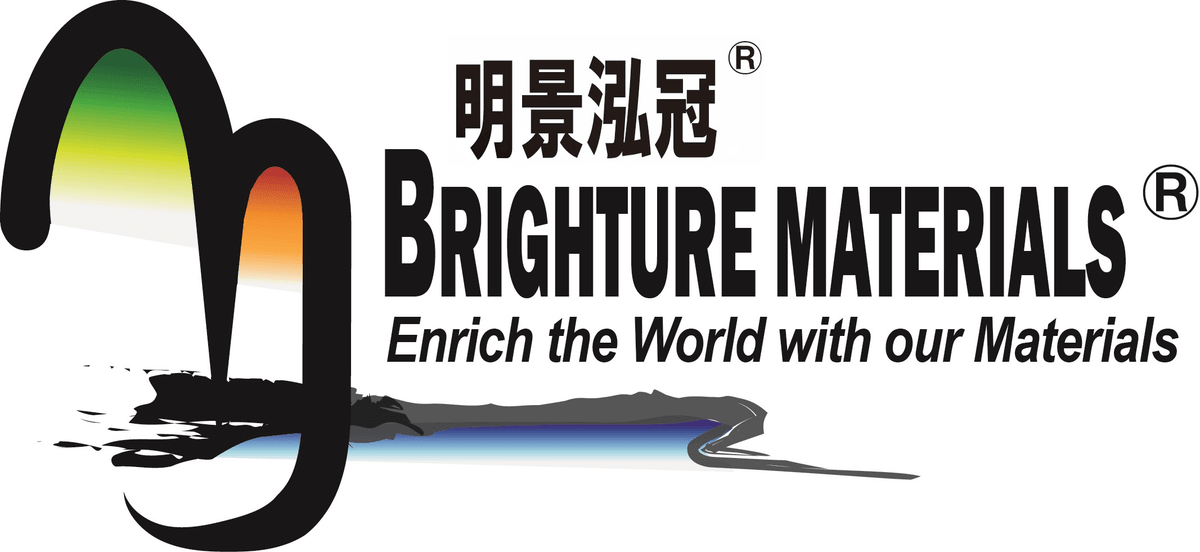
Authorized Dealer of
SAINT-GOBAIN ZIRPRO
- Products
- AM & PM Powder Processing
- Zirconium-Based Products
- …
- Products
- AM & PM Powder Processing
- Zirconium-Based Products
Authorized Dealer of
SAINT-GOBAIN ZIRPRO
- Products
- AM & PM Powder Processing
- Zirconium-Based Products
- …
- Products
- AM & PM Powder Processing
- Zirconium-Based Products
NUA100-pilot Ultrasonic Powder Atomizer
An advanced atomization powder production solution
From alloy manufacturing to powder in just 1 hour!
The NUA100-Pilot is a compact, desktop-sized ultrasonic powder atomizer designed to efficiently
produce small batches of high-quality spherical powders at an affordable price. It targets the same applications as gas atomized (EIGA) powders, without the need for complex infrastructure.
It offers crucibles with varying batch sizes, from 0.3L to 0.8L. The materials are melted and alloyed using an induction heating system (such as graphite crucibles) or a high-temperature direct induction system (ceramic crucibles). The compact ultrasonic atomizer requires minimal space, occupying only a few square meters, including the necessary infrastructure.
Induction Melting
The metal is first melted using induction heating and poured onto a thin metal strip, which is mounted on an ultrasonic generator. The generator causes the strip to vibrate at ultrasonic frequencies, causing the molten metal to break apart into fine droplets. These droplets follow a parabolic path and solidify before hitting the ground. This entire process takes place inside a water-cooled atomization chamber, which is protected by specific gases to reduce or eliminate oxidation. The resulting particles accumulate at the far end of the chamber and fall into a cone and receiver.
Ultrasonic Atomization Process
The ultrasonic vibrations also cause the molten metal to spread into a thin liquid film. When the vibration amplitude reaches a certain threshold, the molten metal is fragmented into droplets, which are ejected from the vibrating surface, forming a mist. This process is similar to how air humidifiers generate water mist. As the molten metal droplets cool, they solidify into spherical powder particles, creating high-quality powder.
4 Simple Steps to Perfect Powder
1Prepare Materials
Place the selected alloys or alloy components into the crucible, ensuring the correct composition for the desired powder characteristics.
2Heat and Melt
The materials are heated to their molten state through precise induction heating, achieving temperatures up to 1800°C to ensure complete melting.
3Atomization
The molten metal is subjected to ultrasonic vibrations, which break the liquid metal into fine, uniform droplets, promoting controlled atomization.
4Powder Collection
The atomized droplets rapidly solidify into spherical powder particles, which are then collected in a containment system for further processing.
The induction melting process is commonly used to handle alloys with melting points up to 1300°C. It is particularly effective for alloys that vaporize easily at these temperatures, such as Sn, Zn, Mg, Pb, and Al-based alloys. Any material, regardless of shape or form, can be placed into the furnace for melting, including alloys, composite alloys, and pure metals.
By adjusting the ultrasonic frequency and controlling the metal liquid flow, the process can achieve precise control over particle size distribution, resulting in fine powders.
Advantages
Prevents Material Loss and Inaccuracies: The system precisely controls the melting temperature through a feedback-based heat control system, reducing material waste and ensuring consistency.
Efficient Atomization: The ultrasonic generator improves the efficiency of atomization, with higher frequency vibrations. This results in effective atomization, even in inert or protective gas environments that prevent oxidation.
Higher Frequency, Higher Output: By increasing the frequency, both production volume and capacity are enhanced. The NUA100-pilot offers exceptional productivity and efficiency in small-scale production, producing batches ranging from 100g to several kilograms.
Flexible Material Shapes: The system does not require specific material shapes. It can process a variety of forms, including pre-alloyed powders and ingots, without the need for complex preparation.
No Complex or Expensive Equipment: Unlike traditional systems, the NUA100-pilot eliminates the need for costly wire-based production equipment, making the atomization process more accessible.
Compact Design with Minimal Space Requirements: The system’s compact size requires only a few square meters of space, including necessary infrastructure, and eliminates the need for additional auxiliary equipment.
Contact
jimmywang@
Tel: (60) 1139 507 160 (Southeast Asia)
(234) 0812 287 8888 (Africa)
©2025 - Copyright Brighture Materials Malaysia / Navector Malaysia. All rights reserved.
Lot 964,Loring Haji Abbas.
Ksmpung Rinching Hilir. 43500 Semenyih.
Selangor, KL Malaysia.